For different types welding works of both electric arc and gas welding, as well as for surfacing and manufacturing of electrodes welding wire, produced in accordance with GOST 2246-70. According to the technical specifications of this standard, the wire is produced in three categories: low-carbon, alloyed and high-alloyed. There are about 80 brands of welding wire.
Also, look at store terms and conditions when considering packaging options. Also, remember that exposed wire is electrically hot when welding. For safety reasons, some stores may prefer closed packaging. Although an open drum may be less expensive than a drum or box, moving parts of a screen can pose a safety hazard. Release costs are another issue for manufacturers.
To save even more, opt for a fully recyclable cardboard box that can be shredded and shredded instead of a wooden or metal coated drum. Items such as lifting straps make it easier for operators to handle packaging. In addition, a wooden pallet underneath the package allows for convenient transport through the forklift. In contrast, integral paper pallets can be more easily damaged by a forklift. Finally, select the packaging that matches the installation layout.
A well-known supplier of welding wire of all categories is Trading House Electrode LLC from Yekaterinburg. TD Electrod will supply welding wire and electrodes not only from domestic manufacturers, but also from leading foreign brands. Currently, 6 kinds of low carbon wire, 30 kinds of alloy welding wire and 40 kinds of high alloy welding wire are produced.
For example, if some of the welding stations are located on the mezzanine. it can be more difficult to pick up and use some types of packages in these bottlenecks. But what if the manufacturer currently uses a stick electrode, flux cored wire, submerged arc, or resistance welding? Benefits include slag-free welding with less cleaning, even with multiple passes.
Alloy wire marking
Other benefits include high efficiency electrode from 97 to 98 percent. Wire placement is the ability of the wire to exit the contact tip at the same location each time for precise placement weld... This can be an important consideration, especially in automated applications.
Alloy wire marking
The welding wire is marked with an alphanumeric code. The first letters CB mean - welding wire. The next two digits are the amount of carbon in hundredths of a percent, then the letter denoting the alloying addition and the numbers corresponding to the amount of the alloying addition in percent. If the amount of alloying additive is less than half a percent, then a number is not put after the letter.
Method for determining the mass fraction of traces of soap grease on the surface of the welding wire
If you want to keep your overall welding costs down, consider the wire price. Saving a penny in the short term can cost you hundreds of dollars in lost productivity in the long run. Remember to select the correct wire for your application, ensure it chemical composition and purchase the best option packaging for the plant where it will be used.
High temperatures have little effect on the toughness and dimensional stability of this alloy. These alloys based on cobalt and nickel have a solid intermetallic phase dispersed in a rigid matrix of eutectic or solid solution. This family of cobalt-based alloys uses chromium and molybdenum as the main alloying elements. They provide good wear resistance with excellent corrosion resistance in reducing environments with hydrochloric, phosphoric and naphthanic acids.
Since chemically pure metal is used extremely rarely, and welding is carried out with alloys, the most widespread is alloyed welding wire. The following metals are used as alloying elements:
- B - niobium
- B - tungsten
- M - molybdenum
- D - copper
- T - titanium
- X - chrome
- N - nickel
- F - vanadium
- C - zirconium
- Yu - aluminum
- G - manganese
Silicon is also used as an alloying element. It is designated by the letter "C". Thus, the SV06X19N9T brand means - welding wire with a content of 0.06% carbon, 19% chromium, 9% nickel and<0,5% титана. Сварочные проволоки с высоким содержанием хрома и никеля предназначены для сварки нержавеющих сталей.
These hardfacing alloys are designed for extremely abrasive and erosive environments. The electrode, arc and weld pool are protected from the atmosphere by an inert shielding gas. The surfacing material is made in the form of a rod. The process can also be mechanized, in which case a manipulator is used to move the workpiece in relation to the welding torch and carbide rod or wire.
Manual deposition of metal arc welding
When done correctly in an overlay, very low iron dilution rates can be achieved. The rod is available in these standard diameters. In this process, an arc is drawn between the coated consumable electrode and the workpiece. The metal core is melted by the arc and transferred to the weld pool as molten droplets. The electrode coating also melts, forming a gas shield around the arc and weld pool and slag on the surface of the weld pool, thus shielding the cooling weld pool from the atmosphere.
Wherever it is used, GOST alloy welding wire determines for which types of alloys this or that type of welding wire is suitable. For example, 2СВ30Х25Н16Г7 - welding alloy wire with a diameter of 2 mm with a high content of chromium, nickel and manganese, should be used for welding stainless high-carbon steels.
Slag must be removed after each layer. Due to the low cost of equipment, low operating costs of the process and ease of transport of equipment, this flexible process is ideal for repair work. The electrodes are available in these standard diameters.
The electrodes are supplied 350 mm long and fit in 0 kg boxes. Depending on the process parameters, the hardness of the welded deposit may vary from the values \u200b\u200bshown in the table above. The wire is also used as a cladding material consumed in the underfloor arc welding process. In this process, a mineral based flux powder flows around the consumable wire and is melted by an arc.
The chemical composition of the filler wire has a major influence on the quality of the welded joint. Proceeding from this and in accordance with GOST, the wire grade is chosen depending on the chemical composition of the alloy being welded.
So for welding low-alloy steels, low-carbon manganese and silicon-manganese welding wires are used - SV-08GS, SV-08GA, SV-10G2, SV-08G2S. For the production of welding with high-alloy steels, a special alloyed welding wire is used: vanadium, titanium, niobium, molybdenum, chromium and nickel.
Wire cables are supplied in these standard diameters. 1, 2 mm - supplied in 15 kg spools 1, 6 mm - supplied in 15 kg spools 2, 4 mm - usually supplied in 25 kg spools 3, 2 mm - supplied in 15 kg spools. Go back for more details.
In addition, due to the highly concentrated heat source, this process is advantageous due to the high powder loading and can achieve very low iron dilution rates in the patch. Since the surfacing materials are in powder form, it is possible to make overlays in many different materials and material combinations with a wide range of hardness and other properties.
The metal is an alloying additive, and its percentage is determined by the chemical composition of the steel being welded.
Wire is used for welding. Currently, there are several varieties of it. Wire with a high level of alloying SV08G2S is one of the demanded types of products. It is used for various types of welding. It is also used as one of the materials in the production of electrodes for surfacing.
Examples of product designation
A deafening noise like an explosion. Sparks are thrown out of the giant cauldron, the smoke rises and gets very hot. The monster in the huge production hall is the electric arc furnace, the heart of the factory. Here, the solid starting material is liquefied within a few minutes. Steel mills are specialized in the production of steel wire. About a thousand tons are produced per year, of which about 300 different qualities work, in which more than 560 people work. The raw materials pass through several stations on their way to the finished wire.
Most often, SV08G2S wire is used when working on welding machines and semiautomatic devices in an industrial environment... Using it, you can carry out manual welding of various steel products. Using this consumable, you can get a high quality welded joint. The seam is smooth and clean.
Applications
The wire of this brand is irreplaceable when performing the following operations:
As a starting material, an iron sponge and scrap are used in different proportions. “Prices and availability are changing almost every month at the moment, so we use both in different volumes,” explains Wrede. Iron ore, which in turn forms the basis for the production of iron sponge, comes by ship from mines abroad. It is supplied in the form of granules in Hamburg. These beads with diameters ranging from 10 to 15 mm are already produced by iron ore producers.
The iron ore must be chemically “reduced” to actual steel production, i.e. the oxygen contained in the iron oxide is removed by reduction to produce pure iron. Some steelworkers perform this step directly in a blast furnace with added coke. In reforming, natural gas is first separated into carbon monoxide and hydrogen.
- the formation of a bead on the seam;
- filling the space between the edges of the workpiece to be welded.
When performing welding work, this hardware is the main element of technological processes. Welding cannot do without it in such areas as:
- construction;
- mechanical engineering;
- aircraft and shipbuilding.
Also note that this alloy welding wire can be used as an effective filler material. One of the salient features is high deposition rate... This ensures high quality performance of complex surfacing activities.
These gases then reduce the iron ore in the reduction plant, producing an "iron sponge". The raw material is melted in an electric arc furnace. The furnace has a huge lid in which graphite electrodes are located. The lid is opened and then the tray is filled from the baskets. Then the lid is closed again and the electrodes are lowered. The arc is now ignited by the current flowing through the graphite electrodes. When the scrap is melted, another iron sponge is added, which also melts. The iron sponge is used proportionally to melt, depending on the desired product properties, but also on the savings.
Recently, high-alloy welding wire has been actively used when working in a gas atmosphere. To create such a medium, argon or a mixture of this gas with others is usually used. Carbon dioxide is often used to form this medium. The choice in favor of the latter is dictated by its lower cost in comparison with argon. When welding is carried out in a carbon dioxide environment, direct current is used. It should be noted that such an environment is recommended for performing works on welded joints of carbon steel products.
For example, it is very advantageous as far as possible to be used to melt, but only so far as is compatible with the desired properties of the product. Electrodes wear out quickly, so they need to be renewed once or twice a day. This causes a power surge when the oven is powered on.
The metalworking must be reported to the transmission network operator a day earlier by the transmission network operator, who can already take action. After about 40 minutes, the iron from the ore or scrap melted. The furnace produces 140 tons of liquid steel per hour. About every hour, 24 times a day, seven days a week, melting occurs.
Requirements for welding wire SV08G2S
In the state standard 2246-70 fixed the technical characteristics and chemical composition of products for welding with this hardware. Normative documents regulate the content in this material of the following elements in percentage:
Then the oven vessel is tilted to the right and left to the side. Slag and molten steel are removed separately. Slag is formed from impurities in the melt, such as calcium, silicon or manganese, which are absorbed by the lime as a liquid slagging agent. It is then processed by a subsidiary, for example, for fertilizers, road construction or the cement industry.
Developed and introduced by the USSR Ministry of Ferrous Metals
The steel is further processed in small ladle furnaces. With the addition of certain additives, it is thus, among other things, alloyed. The liquid metal enters the continuous casting plant from ladle furnaces. This results in so-called blanks up to 14 cm wide, metal blocks 14 cm and 16 m long, which are subsequently stored and then processed into wire products. In the factory, seven pieces are always cast in parallel, which pass through a roller table for cooling.
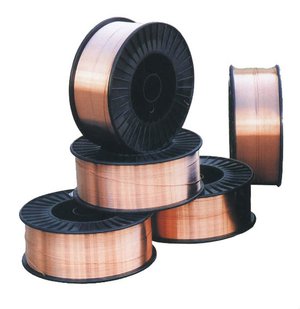
Copper-plated alloyed wire SV08G2S is usually not alloyed with elements such as aluminum, vanadium and a number of others. The presence of manganese in it in an amount from 0.65 to 2.1% is acceptable. Note that this requirement applies only to hardware whose diameter is does not exceed 1.4 mm... If ordinary wire is produced, then the copper content in it cannot be more than 0.25%. The standards allow for the content of up to 0.01% nitrogen in it. Such hardware is used not only for welding, but also for surfacing.
Varieties of alloyed filler materials
Once the blanks have been identified by embossing and embossing, they are magnetically transported and folded as they are magnetic. Subsequently, the blanks are processed in a rolling mill with different wire thicknesses as required. Renewable energy sources such as wind power or photovoltaics today cover 32 percent of electricity demand.
Packaging and labeling
This is having an increasing impact on the electrical grid, as weather-dependent electricity production can no longer be harmonized, and power plants at a fossil level. Accordingly, not only does the price of electricity fluctuate, but the demand for system services also increases in order to maintain the voltage in the grid. “So we are looking into ways to get lower electricity prices or respond to grid fluctuations,” says Wrede. For this purpose, the melting power of the electric arc furnace can be increased by 10 megawatts after adjusting the control, if an excess current is present during production and is accordingly reduced when there is insufficient electrical energy.
Currently, the hardware of this brand is produced with a cross section from 0.3 to 12 mm. Finished products are packed in skeins. The maximum coil weight can be up to 30 kg. Copper-plated wire can be formed into rectangular coils in their cross-section. Their height is 50-90 mm. The inner diameter of this hardware can vary from 100 to 400 mm. As for the outer diameter, it ranges from 175 to 600 mm.
If approved by the consumer, alloy welding wire can supplied in reels or cassettes... Moreover, it must consist of segments without breaks. The product is wound tightly in even rows. The possibility of unwinding or unraveling of the material during transportation should be excluded.
Important characteristics
For alloyed welding wire SV08G2S, the tensile strength should range from 882 to 1372 MPa. Such requirements apply to welding hardware with a diameter of 0.3 to 0.5 mm. For a filler wire with a diameter of 2 mm, this requirement is expressed in a resistance of 686 to 1029 MPa. Conventional and copper-plated wire can be thermally treated if these indicators are not provided by the production technology.
Copper-bonded wire for welding of the SV08G2S brand on its surface has residues of soapy lubricant... It should be said that its presence is not a violation of the requirements of state regulations. Please note that the presence of substances such as sulfur and graphite is permissible in the composition of the lubricant.
Why know the deposition rate?
When performing work on surfacing, a specialist must know what kind of surfacing coefficient the wire used by him has. It should be understood as a value that describes the metal deposited over a specific time at a specific current strength. The deposition rate of hardware is usually is at least 8.5 g / A * h... Its usual meaning depends on:
- chemical composition of hardware;
- type of product coverage;
- polarity and type of current used to perform the surfacing.
The productivity of surfacing operations largely depends on the deposition rate of SV08G2S hardware. Also, this indicator affects the number of losses of the weld to evaporation, as well as to spatter and oxidation. The indicator under consideration also determines the melting coefficient of the base metal, as well as a number of other important characteristics and welding operations.
Deciphering the grade of wire of its dignity
It is not very difficult to understand what the SV08G2S welding wire is. The letters at the very beginning mean welding wire. Figures 08 indicate the content of hundredths of carbon in the wire. The letter G means manganese, and the number after it is the quantitative content of this element in the wire - 2%. Letter C means silicon... If the number after this letter is absent, then this should be understood as the fact that silicon is contained in the wire of the described brand in an amount of less than 1 percent.
The composition of the welding hardware of this brand contains manganese. Thanks to it, an increase in the strength characteristics of the joint is ensured, since this element forms a pronounced crystal lattice of the welded joint. Silicon improves the mechanical properties of the product. For the hardware described in this article, the content of silicon and manganese is optimal (0.83 / 1.95). Thereby provides a number of advantages its application for surfacing operation:
- its use allows you to get a high quality connection;
- hardware provides high strength characteristics of the seam;
- thanks to it, the minimum cost of manufacturing the welded material is ensured;
- the hardware of this brand has a stable and chemical composition.
Conclusion
When performing welding, one cannot do without using a welding wire. It allows you to create a high-quality welded joint. Currently available on the market a large number of brands welding wire. Many specialists use SV08G2S hardware when performing welding work. Thanks to the components included in the composition, its use allows you to perform high-quality welding work and obtain a reliable welded joint.